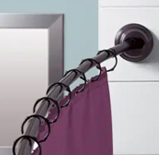
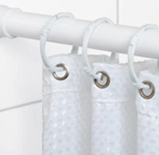
Tube Cutting
Tubular components/products are cut to specific lengths or shapes. Cutting methods such as Automatic Pipe Cutting is used. Our range includes pipes from 9mm to 50mm in diameter with wall thickness from 0.3mm to 3.0mm. The material handled by us include mild steel, stainless steel, aluminum.
Machining
Machining processes like drilling, tapping, milling, and turning are used to create precise holes, threads, or other features on tubular components/products..
Tube Forming
The tubular components/products are formed and shaped. Processes include end forming, tube bending and tube twisting.
Surface Treatment
Components/products undergo decorative surface treatment processes such as polishing, plating, painting, or powder coating. The finishes are subjective to various industry specific tests to ensure good appearance and longevity.
Assembly
Tubular components/products are assembled with other components or sub-assemblies using techniques such as brazing, soldering, adhesives, or mechanical fastening to create a finished product.
Cutting
Sheet metal is stamped or laser cut. This involves use of mechanical presses of various capacities as per the metal thickness.
Forming
Various type of forming processes are used to give final shape to the products. This includes drawing, bending , spinning, hydro forming.
Welding
Sheet metal components/products may require welding to join multiple pieces of sheet metal together or to attach other components. Welding methods such as MIG (Metal Inert Gas) welding, TIG (Tungsten Inert Gas) welding, or spot welding are used, depending on the material and application requirements.
Machining
Machining processes such as drilling, milling or tapping are used to create precise holes, threads, or other features on sheet metal components/products. CNC (Computer Numerical Control) machines are commonly used for high precision and complex sheet metal parts.
Surface Treatment
Components/products undergo decorative surface treatment processes such as polishing, plating, painting, or powder coating. The finishes are subjective to various industry specific tests to ensure good appearance and longevity.
Assembly
Sheet metal components/products are assembled with other components or sub-assemblies using techniques such as welding, brazing, riveting, or mechanical fastening to create a finished product.
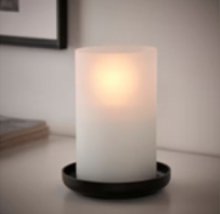
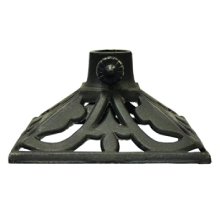
Die Preparation
The first step in aluminum die-casting is to prepare the die, which is a specialized tool made from high performance steel that is used to shape the molten aluminum into the desired component/product. Die preparation involves machining the die to the desired shape.
Alloy Melting
Aluminum alloys are melted as per desired metallic composition in a furnace to a specific temperature, typically above the melting point of aluminum (660°C or 1220°F), to create molten aluminum that is suitable for die-casting.
Die Casting
The molten aluminum is then injected into the die at high pressure using a machine called a die-casting machine. The high pressure helps to fill the die and solidify the molten aluminum quickly, taking on the shape of the die to form the desired component/product. Our machine capacity ranges from 180 tons to 400 tons.
Cooling and Ejection
Once the molten aluminum has solidified in the die, the die is cooled to further solidify the component/product. Once the component/product has cooled and solidified, it is ejected from the die using ejector pins or other mechanisms.
Trimming and Finishing
After ejection from the die, the component/product may undergo trimming and finishing processes to remove excess material, smooth edges, and achieve the desired surface finish. These processes may include trimming, deburring, grinding, sanding, or polishing.
Machining and Secondary Operations
Some aluminum die-casted components/products may require additional machining or secondary operations, such as drilling, tapping, or machining of threads, to achieve the desired features and tolerances.
Surface Treatment
Components/products undergo decorative surface treatment processes such as polishing, plating, painting, or powder coating. The finishes are subjective to various industry specific tests to ensure good appearance and longevity.
Cutting and Handling
Aluminum extrusions are bought from third party vendors. They are cut on our automatic machine using carbide saws. Our range includes profiles as low as 9mm to as high as 180mm in diameter.
Machining and Fabrication
Aluminum extrusion profiles may require additional machining or fabrication processes to achieve the desired features, tolerances, or assembly requirements. These processes may include cutting, drilling, tapping, milling, or other machining operations.
Surface Treatment
Components/products undergo decorative surface treatment processes such as polishing, plating, painting, or powder coating. The finishes are subjective to various industry specific tests to ensure good appearance and longevity.
Die Preparation
The first step in plastic molding is to prepare the die, which is a specialized tool made from high performance steel that is used to shape the molten aluminum into the desired component/product. Die preparation involves machining the die to the desired shape.
Material selection
The appropriate plastic material is selected based on the requirements of the component, including factors such as strength, flexibility, heat resistance, and cost.
Material preparation
The selected plastic material is then prepared for the molding process. This involves processes such as drying, blending with additives, and melting to achieve the correct viscosity for injection into the mold.
Injection molding
The plastic material is injected into the mold cavity under high pressure using an injection molding machine. The molten plastic fills the cavity, taking on the shape of the mold. The plastic is allowed to cool and solidify within the mold, forming the desired component shape. Our capacities of machines varies from 60 tons to 400 tons.
Finishing
The molded component undergoes additional processes such as trimming, deburring, and surface treatment to remove any excess material, smooth rough edges, and improve the appearance and functionality of the final product.